Jet engine vibration is a key safety and efficiency concern in aviation. Unchecked vibration can cause issues from cabin noise to catastrophic failures. Engineers use vibration analysis and trim...
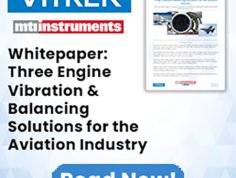
This site is operated by a business or businesses owned by Informa PLC and all copyright resides with them. Informa PLC's registered office is 5 Howick Place, London SW1P 1WG. Registered in England and Wales. Number 8860726.
Aviation Week Marketplace is part of the Informa Markets Division of Informa PLC
Save this service to your Saved Items and return to it later.
Jet engine vibration is perhaps the worst enemy of an aircraft maintenance team. Out-of-balance parts can lead to cracked fan, turbine and compressor components; general metal fatigue; and if unchecked, catastrophic engine failure.
Overall vibration, however, is actually the summation of vibration contributions from any combination of moving parts within the engine, which makes analysis and balancing extremely complicated. Structural characteristics of individual aircraft compound the problem.
Engine location on the airframe or type of engine mount, for example, can transmit or magnify vibration troubles. Let’s take a look at some of the industry-wide challenges to aviation safety and service.
What Causes Engine Vibration?
Engine vibration is mainly caused by imbalance. Asymmetrical mass distribution in rotating components creates uneven centrifugal forces, leading to vibration. Testing often reveals that vibration is due to rotor imbalance, worn parts (like pumps or bearings), or both. Vibration & Balancing test systems are used to check vibration levels and balance rotors.
How Does an Aircraft Engine Become Unbalanced in the First Place?
Out-of-balance conditions can arise from various causes, including replacing rotating engine parts like fan blades, damage from bird strikes or impacts, and natural wear and corrosion over time.
How Should an Aircraft Engine be Tested for Vibration, and How Often?
Engine manufacturers provide a maintenance schedule, and the FAA issues safety directives with specific testing requirements and vibration limits. Some airlines may impose stricter schedules and limits. Engines should be tested as per the schedule, after impact events, or if vibration levels increase.
Who is Responsible for Performing Routine Engine Vibration Analysis & Balancing?
Aircraft operators are responsible for ensuring safety and standards. Commercial airlines may use in-house maintenance crews, OEM maintenance contracts, or third-party MRO providers like Lufthansa Technik, HAECO, and Delta Tech Ops for engine maintenance. The military also uses its own crews and contracted services for maintenance and repairs.
What Role Does Vibration Analysis & Balancing Play In An Engine Lifecycle Management Plan?
Turbine engines have OEM-specified vibration limits, and manufacturers provide procedures to address out-of-spec vibration. These procedures’ effectiveness depends on the test equipment and personnel skill. With proper tools and training, engines can be brought within limits without needing an engine change.
Significant cost savings are possible with the latest vibration analysis and trim balance procedures. Traditional fan-only balancing methods require multiple engine runs, while new precision systems can achieve minimal vibration in one run. Early turbine vibration analysis with advanced portable systems can also prevent engine removal and replacement.
Learn more by downloading our FREE Whitepaper titled Three Vibration/Balancing Solutions for the Aviation Industry!
View this product at bit.ly/3tgyk1u
Jet engine vibration is a key safety and efficiency concern in aviation. Unchecked vibration can cause issues from cabin noise to catastrophic failures. Engineers use vibration analysis and trim...
MTI’s premier training program provides specifics for your environment and engine type. With proper training, a post maintenance engine vibration test should be reduced to two hours or less; versus...
The TSC-4800A is versatile and capable of working with a wide range of engine types, including turbofan, turboprop, industrial, and power generation equipment. Versatile Signal Conditioning:...
The Vitrek Automated Cable Test Suite lets you test faster and more reliably. By pairing Vitrek’s accurate hipot testers with a 964i high-voltage switch you can reconnect the active probes in...
The New PBS eXpress provides most of the features available in upscale large turbine engine on-wing balancing products, but is redesigned specifically for corporate aviation MRO needs — providing...